VIKING JOHNSON- FUTUREPROOF WELDING TECHNIQUES BENEFIT THE CUSTOMER
March 4, 2011
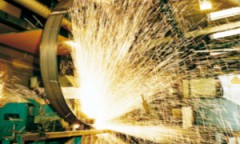
Viking Johnson is a world leader in the manufacture and supply of couplings, flange adaptors and pipe repair solutions for the international water, wastewater and gas markets. The Company manufactures steel sleeves and end rings, on its 14 acre manufacturing facility in Hitchin, for a wide range of dedicated and wide tolerance couplings. These products have a design life of 50 years and will form a crucial part of a distribution network. To ensure the future integrity of a pipeline, it is vitally important that all welds are structurally sound and dimensionally stable.
Viking Johnson is one of the few manufacturers, around the world, that utilises the Flash Butt Welding technique for joining sleeves and rings together to ensure that the product will stand the test of time.
Flash weldingis a type of resistance welding that involves pressing two ends together, while simultaneously running a current between them. This has the effect of forming a seamless joint between the two metals that is free of oxides.
This process has many advantages. It consistentlydelivers a quality weld, offering the best solution with regard to weld penetration, and cleanliness of the interfaces.
Furthermore, the post welding cold expansion process creates dimensionally stable rings of repeatable quality, essential for the consistent compression of the annular gasket.
The benefit to customers is a first class coupling with a ‘solid state weld’ which will meet the required design life.
However, flash butt welding demands a high capital cost for purchasing, installing and setting up the equipment, which is why many companies prefer to use the less expensive, but less reliable Arc Welding process. Arc welding, has many disadvantages for the end user. There is a significant risk of product / performance variation and so various tests need to be managed by ‘highly skilled operators’ to ensure the integrity of the weld is sound.
In contrast, the flash butt welded joint is considered a ‘solid state weld’ where internal defects are very rare’ However, Viking Johnson goes one step further, (in line with AWWA C219 standards) by cold expanding all section welds to typically 1% beyond yield to prove the integrity of the joint. This process also has the added benefit of ensuring a correct ring shape and internal diameter whilst further strengthening the material. The correct shape and diameter of the ring is of course essential to minimise the possibility of leakage.
Couplings Designed for a Long Life
Viking Johnson has its own design team, utilising the latest engineering software and in-house test facilities and for the last 80 years has delivered products that exceed market expectations. In addition to the required
Industry specifications, Viking Johnson products also undergo accelerated ageing tests, which ensure a design life of 50 years, providing the customer with complete peace of mind.
For more information please contact Simon Shand-Brown, Group Marketing Communications Manager on 01473 277300 or sshand-brown@crane-ltd.co.uk.
Enhanced Product Integrity from Viking Johnson- Arab Water World- July 2011